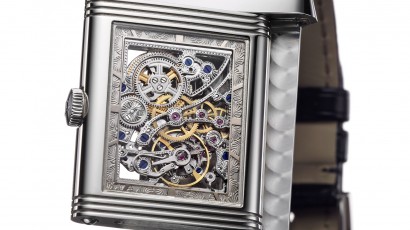
What You Need To Know Before Buying A Watch
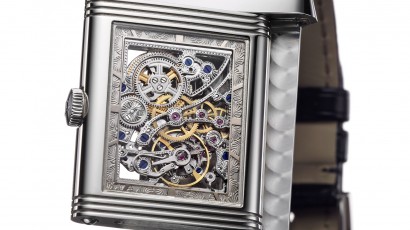
Jaeger LeCoultre
“Art Deco watches were arguably some of the most beautiful ever produced.“
Artistry in watchmaking is not only in the movement. An expertly beveled shoulder or contrasting brushed and polished surfaces on a watchcase can be equally eye-pleasing and far more visible. And while case manufacturing is not as much of a micro-engineering marvel as a watch movement, it can be equally technical and difficult to master.
The primary role of the watchcase is to protect the movement from the elements — heat, moisture, dust, body fluids. But that’s the easy part, thanks to modern gasket materials and the tight tolerances that can be achieved with modern manufacturing. The hard part is designing a case that states the watch’s purpose with good proportions and the interplay of finished surfaces.
Early wristwatch cases were built by simply welding a curved strap bar onto each end of a pocket watchcase, around which leather strap pieces were riveted. This design made for fairly unimaginative case shapes until the late 1920s and ’30s, when integrated “horns,” or “lugs,” were introduced. Watch builders were then able to play with the flow of the case into the lugs, adding twists and flourishes, freed from the constraints of mere function.
Art Deco watches were arguably some of the most beautiful ever produced. The most famous of this era was the Jaeger-LeCoultre Reverso, a rectangular masterpiece of angles and steps. The Reverso namesake piece de resistance was the reversing case that hid the watch dial from view to protect it from damage during polo matches. The Reverso is still popular today, proof that great design never goes out of style.
As the decades progressed, cases became more varied in shape and size. Whereas in earlier times, when watches rarely exceeded 34 millimeters in diameter, by the late 1960s, brands like Rolex and Omega were creating sports watches up to 40mm across. The shapes of this time period created what could be considered the archetypal wristwatch shape — a round case body flowing into curved lugs that drape down onto the wrist. Some lugs were “twisted” into a lyre shape, such as on the later Omega Speedmasters, while Rolex took a more slab-sided approach on. Where surfaces adjoin, often one is polished to a high shine while the other is a matte brushed finish, creating visual interest and light play. These techniques are still used today.
Where watchcases really came into the modern era was in the use of new materials. Traditionally, cases were made of stainless steel or gold, either plated or solid. Now we see cases made from titanium, ceramic and even sapphire. These materials have properties beneficial to watches — magnetism, corrosion and scratch-resistant — but they are extremely difficult to work with. IWC Schaffhausen was the first brand to really master the use of titanium and ceramic back in the 1980s and ’90s, and this past year saw high-end watchmaker Richard Mille build a completely see-through sapphire case. Creating these cases would have been a mere dream to the case builders of an earlier age, made possible now by state-of-the-art design and manufacturing techniques.
What’s next for watchcases? No one knows, though we may have seen a glimpse with the Cartier Concept One watch with its vacuum-sealed clear ceramic case. Next time someone tells you that only the movement matters when it comes to watches, tell him to think again and consider the case.